Cold drawing by Gardette
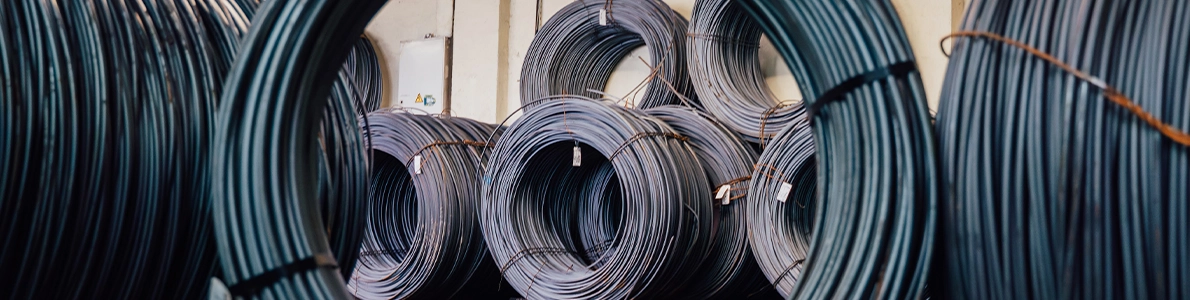
Exploring cold-drawing: Benefits and the complete process
- What is cold drawing?
- The complete drawing process
- Why trust Gardette for your profile bars and coils rather than a simple reseller?
What iscold drawing?
L'étirage à froid est une technique de fabrication utilisée dans l'industrie pour la production de barres ou de profils métalliques. Le processus d’étirage a pour objectif de réduire la dimension d’un matériau pour lui donner une forme bien précise. Pour cela nous passons par plusieurs étapes :
- Reducing the cross-section of the raw material by making a silk (reducing the end of the raw material)
- Then we pass through a die also known as a matrix.
- Finally, the cold-drawing machine pulls the material with carriages, thus obtaining a reduced size with very precise dimensional dimensions and enhanced mechanical characteristics.
In this article, we'll take a closer look at this technique and the advantages it offers.
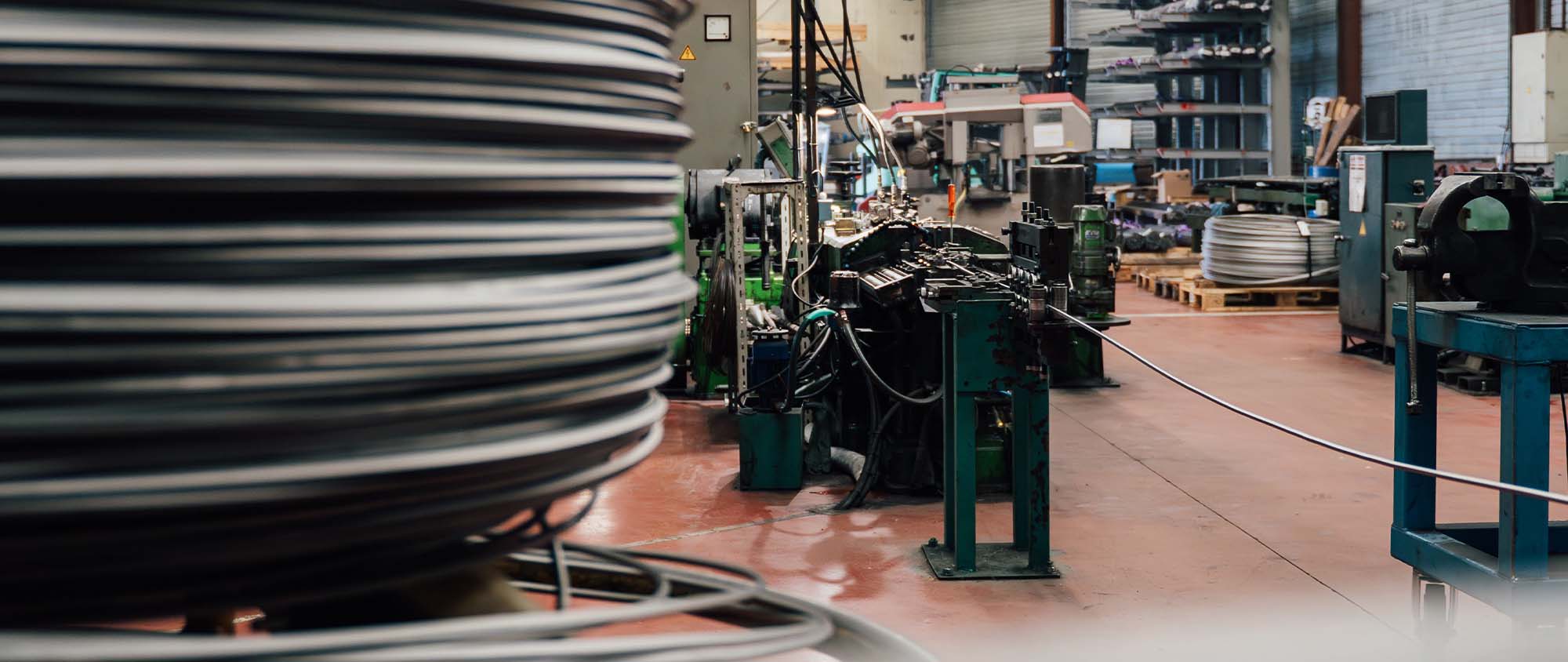
The complete drawing process
L'étirage est un processus de production en plusieurs étapes. Tout d'abord, le matériau brut est choisi en fonction des spécifications requises pour le produit final.
Les matériaux les plus couramment utilisés dans l'étirage à froid sont l'acier et l’inox qui sont eux-mêmes subdivisés en une multitude de déclinaisons.
Step 1: Stripping
We mechanically blast the material = The aim of this operation is to prepare the material for cold forming by eliminating the potential presence of scale on the raw material to be stretched. This step involves projecting abrasive particles onto the surface of the material to remove surface defects and improve the adhesion of coatings.
2nd stage: cold rolling
This stage consists of transforming the prepared material in a rolling mill, which shapes it into the desired form and produces a semi-finished product.
The aim is to deform the material to obtain a shape different from that of the raw material.
Rolling also produces more precise profiles and more consistent dimensions. The machines used for lamination are equipped with rollers specially designed to guarantee optimum lamination quality.
Step3: Heat treatment of the material
In order to release the stresses released during cold rolling of the material and obtain structures that meet customer requirements, we pass the semi-finished product through a coil or bar furnace for heat treatment.
4th stage Shot blasting
We'll once again strip the material to remove any traces of scale and prepare it for cold forming.
Step 5: Cold drawing
The final stage in the manufacturing process is cold drawing. This stage consists of :
- pull the raw material through a narrow die using carts.
- It is then straightened using rollers.
- Finally, it is sheared to the desired length.
The material is drawn to a reduced size and precise shape. This operation also improves the strength and quality of the material, with optimal mechanical properties and increased resistance.
At Gardette, bars and profiles range from 3 to 4 meters, and we also offer coil drawing.
By combining these processes, we are able to obtain solid products that are :
- Des barres carrées, ronds ou méplats avec une précision mécanique excellente
- Metal profiles without material removal
- High-performance drawn coils for small dimensions
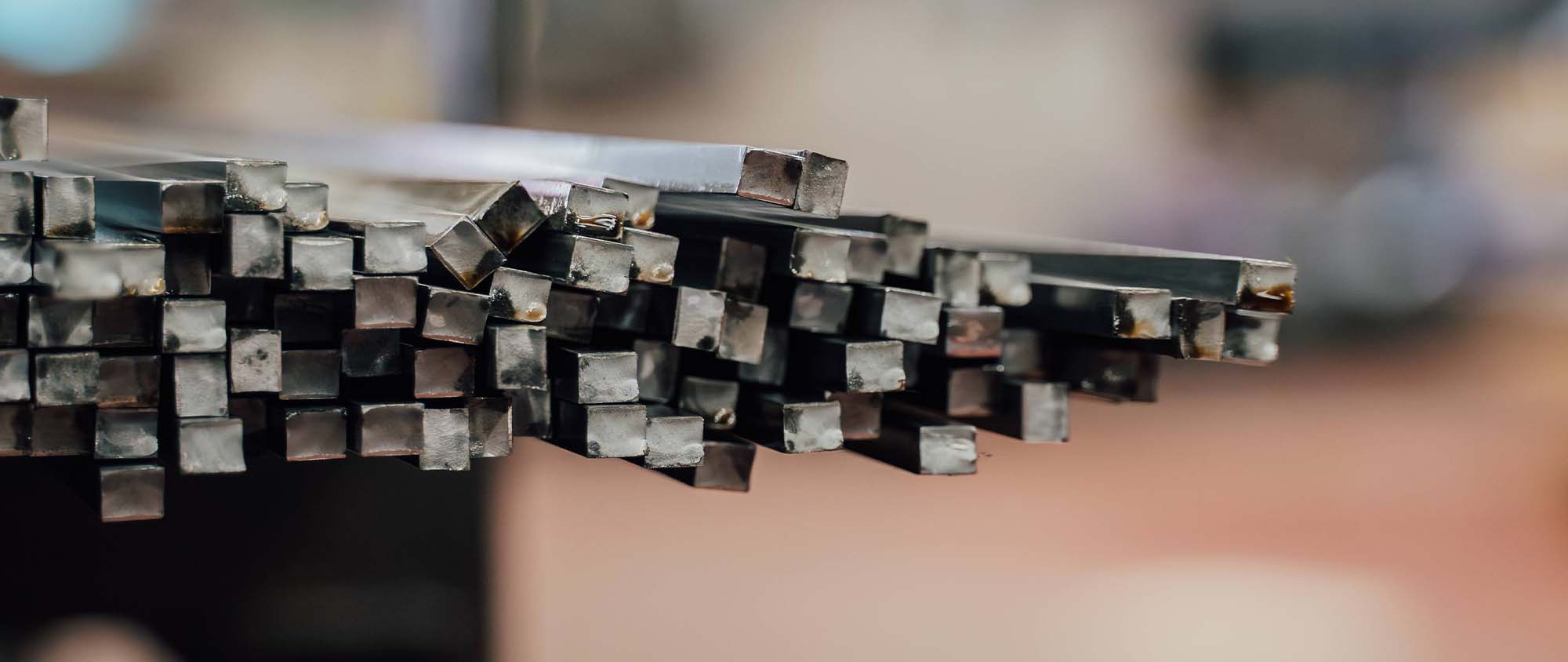
Why trust Gardette for your profile bars and coils rather than a simple reseller?
Our key responsive manufacturing structure enables us to be as flexible and reactive as a reseller, since we manufacture our own materials and are therefore specialized and versatile.
What's more, we draw 100% of the material in France, which has the advantage of guaranteeing superior material quality and complete traceability of the manufacturing process.
Nous sommes le seul fabricant de clavettes au monde à maîtriser l’étirage à froid conformément aux normes qualité en vigueur (NF EN 10277-DIN 6880).
We are committed to finding an answer to your problem in less than 7 days.
Contact us